Proses Reaktörleri
Hidrojenasyon, esterifikasyon ve trans-esterifikasyon, otoklav, dozatör ve benzeri kesikli ve sürekli reaktör sistemlerinin kurulumu, tasarım sürecinden devreye alınmasına kadar firmamız tarafından komple anahtar teslim olarak gerçekleştirilmektedir. Teklif onayından itibaren hem tasarım sürecinde ve hem de ürün teslimi sonrasında kimyasal ve mekanik danışmanlık hizmeti verilmektedir.
Kimyasal proses ihtiyacınıza uygun reaktör sistemi, deneyimli mühendis kadromuz tarafından 3D çizimler ve akış diyagramlarıyla tasarlanarak imal edilir ve testleri ardından devreye alınır. Tasarımın en ince detaylarına kadar verim, işletme kolaylığı, süreklilik ve görsellik unsurları esas alınır. Talep edildiği takdirde tasarım ve test incelemesi gerçekleştirilerek ürün için CE sertifikalandırması yapılabilmektedir.
Reaktör Özelliklerimiz
- (5 – 35.000) litre kapasitelerde
- (-0,8 – 150) bara basınçlarda
- (-60 – 850) °C sıcaklıklarda
- (0 – 1000) rpm karıştırıcı devirlerinde
- Manyetik kaplinli yada mekanik veya yumuşak salmastralı
- Ceketli veya serpantinli ısıtma ve soğutma
- Hollow-shaft veya vortex gibi özel karıştırıcılı
- Dolgulu kolon, kondenser ve dekantörlü
- CE Sertifikalı (opsiyonel)
Not : Detay açıklamalar için lütfen proses isimlerine tıklayın.
Reaksiyona tabi tutulacak hammadde, sıvı ve katı katalizörler reaktöre dozajlandıktan sonra hidrojen gazı ile kısmi basınçlandırma gerçekleştirilir. Ceket veya serpantin sistemi ile gerekli sıcaklığa çıkarılan yüksek basınçlı reaktörde, basınç kontrollü hidrojen beslemesi ile reaksiyon başlatılır. Çözelti içerisine gaz dispersiyonunu en iyi şekilde sağlayan karıştırıcı sistemiyle de prosesin hızlı ve verimli bir halde gerçekleşmesi sağlanır. Reaktör tasarımındaki en önemli parametreler; gaz sarfiyatsız efektif karıştırma sistemi ile yüksek basınç ve sıcaklık ortamında hidrojen sızdırmazlığıdır.
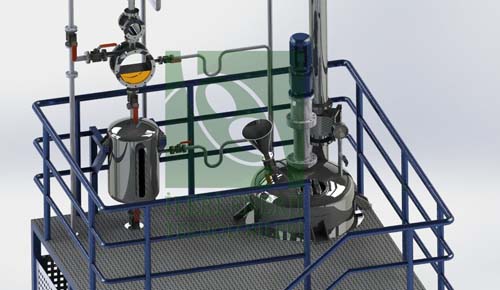
Esterifikasyon reaktörü içerisine beslenen asetik asit, butil alkol ve konsantre slfirik asit karıştırılarak esterifikasyon dengesi sağlanana kadar ısıtılır. Esterifikasyon dengesine ulaşıldığında reaksiyonlar sonucu oluşan su, buharlaştırılarak sistemden ayrıştırılır. Prosese su oluşumu bitene kadar devam edilir ve esterleşme gerçekleştirilmiş, butil asetat üretilmiş olur. Reaksiyondan çıkan fazla hammaddelerin geri kazanımı, butil asetatın saflığı ve enerji verimi sistemin önemli hususlarıdır.
Trans-esterifikasyon Sistemi (ör. Alkid Reçinesi Üretimi)
Trans-esterifikasyon prosesinin bir örneği olan alkid reçinesi üretiminde, reaktöre beslenen poliol (ör. pentaeritritol) ve yağ, katalizör eşliğinde karıştırılarak istenilen proses sıcaklığına ısıtılır. Ardından kısmi olarak soğutulan çözelti içerisine dikarboksilik asit veya karboksilik asit anhidrit (ör. ftalik anhidrit) eklendikten sonra tekrar ısıtılır ve polyester alkid reçinesi oluşturulur. Su, uygun bir solvent (ör. ksilol) ile birlikte buharlaştırılarak çözeltiden uzaklaştırılır, buharlar yoğuşturulduktan sonra solvent sudan ayrıştırılarak reaktöre geri beslenir. Reaksion boyunca çözelti asiditesi ve viskositesi ölçülür. Kullanılan yağ, asit ve poliol değiştirilerek birçok farklı alkid reçinesi sentezlenebilir. Isıtma ve soğutma kontrolü, karıştırma etkinliği ve solvent geri kazanımı prosesin teknik unsurlarıdır.
Silisyum oksit (silis kumu), sodyum hidroksit (kostik) (potasyum silikat için potasyum hidroksit) ve suyun basınç altında ısıtılarak karıştırılmasıyla üretilen sodyum silikat, deterjan üretiminden alçıpan yapımına kadar birçok alanda kullanılmaktadır. Dozatör, karıştırıcılı otoklav, dinlendirme tankı, filtrepres ve ürün tankı olmak üzere beş aşamada üretim sağlanır. Dozatör ve karıştırıcılı otoklav reaktörünün dizaynı, verimi ve proses süresini etkileyen en önemli unsurlardır.
Formaldehit Reçinesi Üretim Sistemi
Metanol buharının gümüş katalizör içerisinden geçirilip suda çözündürülmesiyle elde edilen formaldehit çözeltisi reaktöre beslenir ve ısıtılır. Alkali ve üre (veya fenol veya melamin) ilavesinden sonra pH kontrolü ile birlikte reaksiyon sıcaklığına ısıtılır ve polimerleşme sağlanır.